Quality Assurance Tests
Raw Materials Testing
1. Mechanical Test - Assures raw materials compliance to tensile strength of 80,000 PSI
2. Base Metal Thickness Test - Assures raw materials compliance to thickness
Quality Compliance Tests
These tests assures APO Galfan’s compliance to various International Standards
1. Coating Mass Test - Monitors the weight of the Galfan coating
2. Coating Mass Composition Test - Ensures the 95% zinc & 5% aluminum alloy composition
3. Reverse Impac & T-Bend Test - Assures that the galfan coating meets superior adhesion qualities
Quality Assurance Tests
Physical tests conducted for Paint’s Dry Film ( After processing in the CCL, all prepainted coil are tested.)
1. Reverse Impact & T-Bend Tests - Are the ultimate tests that ensure paint adhesion and flexibility.
2. Paint Inspection Gauge & Micrometer Test - Ensures the desired paint thickness is achieved.
3. Accelerated Weather & Environmental Exposure Test - Determines total paint performance in different weather.
4. Chemical Resistance & Solvent Resistance - Are reliability tests that monitors and evaluates the reaction of the Total Paint system when exposed to various hazardous & chemical environments.
4. Gloss meter & Hunter Lab UV Test - Ensures the aesthetic consistency of the painted product for its designed life cycle.
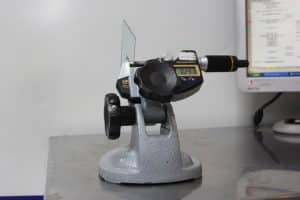
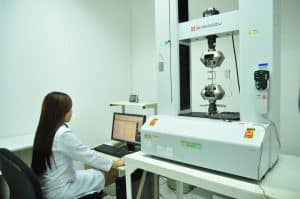
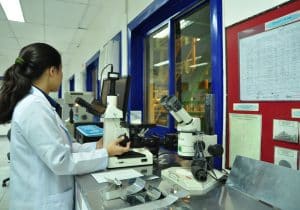
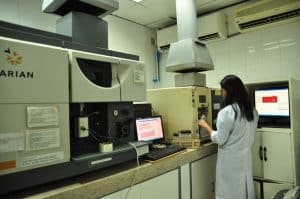
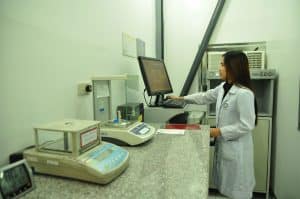
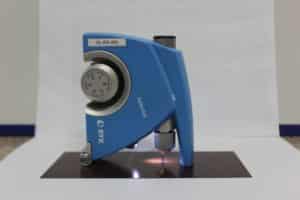
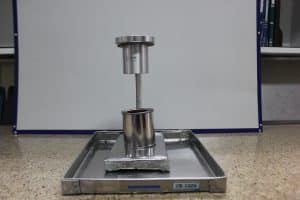
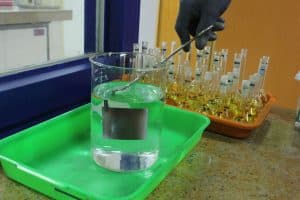
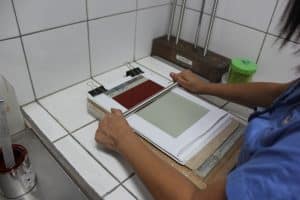
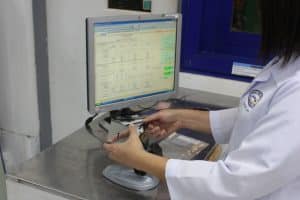